Visualiza nuestros
catálogos formativos:
-
Certificados de profesionalidad
- Gestión Empresarial y Recursos Humanos
- Formación, Educación y Orientación Laboral
- Servicios a la Comunidad
-
Sanidad, Dietética y Nutrición
- Dietética y Nutrición
- Acción Social y Ética
- Atención Domiciliaria
- Ciencias Sanitarias
- Fisioterapia
- Geriatría y Gerontología
- Laboratorios
- Medicina Alternativa / Naturopatía
- Odontología
- Óptica
- Psicología Infantil
- Radiología
- Transporte Sanitario
- Urgencias y Emergencias
- Veterinaria
- Enfermería
- Logopedia
- Psicoterapia y Psiquiatría
- Análisis Clínicos
- Primeros Auxilios
- Farmacia
- Gestión Sanitaria
- Personal Sanitario
- Sexología
- Electromedicina
- Trabajo Social
- Auxiliares de Enfermería
- Celador
- Ergonomía
- Idiomas
- Prevención de Riesgos Laborales, Calidad, Medioambiente, I D I
- Informática y Programación
- Inmobiliaria, Arquitectura e Interiorismo
- Energías Renovables y Agua
- Formación Profesional y Oficios
- Actividad física y del Deporte
- Seguridad y Vigilancia
- Hostelería y Turismo
- Agraria
- Imagen Personal
- Maquetación y Artes Gráficas
- Edificación, Obra Civil e Industrias Extractivas
- Comercio y Marketing
- Derecho y Aspectos Jurídicos
- Creación, Diseño y Edición Digital
- Industria Alimentaria y Restauración
- Transporte y Mantenimiento de Vehículos
- Instalación, Mantenimiento y Fabricación Mecánica
- Maquinaria
- Juegos de Azar
- Artes y Artesanía
- Especialidades Formativas
- Sanidad, Dietética y Nutrición
- Gestión Empresarial y Recursos Humanos
-
Formación, Educación y Orientación Laboral
- Escuela de Padres
- Orientación Laboral
- Formación E-learning
- Formación Permanente del Profesorado
- Formador de Formadores
- Pedagogía Terapéutica
- Educación
- Comedores Escolares
- Guarderías y Educación Infantil
- Lengua de Signos
- Logopedia
- Nuevas Tecnologías en Educación
- Transporte Escolar
- Bibliotecas
- Musicoterapia
- Servicios a la Comunidad
-
Sanidad, Dietética y Nutrición
- Dietética y Nutrición
- Manipulador de Alimentos
- Acción Social y Ética
- Atención Domiciliaria
- Ciencias Sanitarias
- Fisioterapia
- Geriatría y Gerontología
- Laboratorios
- Medicina Alternativa / Naturopatía
- Odontología
- Óptica
- Pediatría y Puericultura
- Psicología Infantil
- Quirófano
- Radiología
- Transporte Sanitario
- Urgencias y Emergencias
- Veterinaria
- Alergología
- Cirugía Ortopédica y Traumatología
- Dermatología
- Enfermería
- Endocrinología
- Neurología
- Otorrinolaringología
- Psicoterapia y Psiquiatría
- Homeopatía
- Análisis Clínicos
- Primeros Auxilios
- Microbiología
- Farmacia
- Gestión Sanitaria
- Personal Sanitario
- Sexología
- Terapia Ocupacional
- Biotecnología Sanitaria
- Electromedicina
- Trabajo Social
- Auxiliares de Enfermería
- Celador
- Ginecología
- Oncología
- Acupuntura
- Ergonomía
- Vendajes
- Vendajes Neuromusculares
- Idiomas
- Prevención de Riesgos Laborales, Calidad, Medioambiente, I D I
- Informática y Programación
- Inmobiliaria, Arquitectura e Interiorismo
- Energías Renovables y Agua
- Formación Profesional y Oficios
-
Actividad física y del Deporte
- Ocio y Tiempo Libre
- Medicina Deportiva
- Dirección de Instalaciones, Entidades Y Eventos Deportivos
- Educación Física
- Buceo
- Natación
- Caza
- Socorrismo Acuático
- Actividades acuáticas
- Fútbol
- Baloncesto
- Atletismo
- Pádel
- Balonmano
- Pilates
- Fitness
- Ciclismo
- Fitness musical
- Yoga
- Anatomía deportiva
- Ciclo Indoor
- Rehabilitación Deportiva
- Senderismo
- Gimnasia para Mayores
- Seguridad y Vigilancia
- Hostelería y Turismo
- Agraria
- Imagen Personal
- Maquetación y Artes Gráficas
- Edificación, Obra Civil e Industrias Extractivas
- Comercio y Marketing
- Derecho y Aspectos Jurídicos
- Creación, Diseño y Edición Digital
- Industria Alimentaria y Restauración
- Transporte y Mantenimiento de Vehículos
- Instalación, Mantenimiento y Fabricación Mecánica
- Maquinaria
- Juegos de Azar
- Artes y Artesanía
- Oposiciones
Áreas Formativas
- Inicio >
- Certificados de profesionalidad>Instalación, Mantenimiento y Fabricación Mecánica>Fabricación Mecánica>Curso de Fabricación por Abrasión, Electroerosión, Corte y Conformado, y por Procesos Especiales
Curso de Fabricación por Abrasión, Electroerosión, Corte y Conformado, y por Procesos Especiales


Ahora aprovéchate de un 20% de descuento en la versión online con la compra del material a distancia.
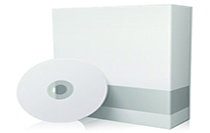
2
1
Manual teórico MAN_EU_3587 |
Fabricación por Abrasión, Electroerosión, Corte y Conformado, y por Procesos Especiales Vol. 1 | |
Manual teórico MAN_EU_3590 |
Fabricación por Abrasión, Electroerosión, Corte y Conformado, y por Procesos Especiales Vol. 2 | |
Cuaderno de ejercicios CEJ_EU_3352 |
Fabricación por Abrasión, Electroerosión, Corte y Conformado, y por Procesos Especiales |
UNIDAD DIDÁCTICA 1. INTERPRETACIÓN DE DOCUMENTACIÓN TÉCNICA PARA EL MECANIZADO
- Planos
- Tolerancias geométricas simbología, interpretación
- Tolerancias dimensionales
- Cálculo de los valores de tolerancia para ejes y agujeros
- Calidades superficiales
- Catálogos comerciales de herramientas
- Consultas de condiciones de trabajos
- Interpretación de un proceso de mecanizado
UNIDAD DIDÁCTICA 2. MÁQUINAS Y SUSTANCIAS ABRASIVAS
- Rectificadora plana, cilíndrica, sin centros, de perfiles, especiales
- Esmerilado. Máquinas de esmerilar
- Afiladora universal
- Formas geométricas obtenibles
- Máquinas acabadoras y operaciones
- Abrasivos. Definición y clases
- Tipos de muelas
- Características de una muela
- Condiciones de corte en el rectificado
- Montaje de las muelas. Precauciones generales
- Proceso y utilidad del equilibrado
- Reavivado y perfilado de muelas
- Fluidos de corte. Tipos y aplicaciones
- Precauciones en el uso de las muelas
- Precauciones en el almacenaje de las muelas
- Sistemas de fijación de piezas
- Dispositivos de las máquinas herramienta
- Mecanizado por electroerosión
- Técnica de mecanizado por electroerosión
- Material más común del electrodo
- Fijación de pieza y electrodo
- Centraje y alineación del electrodo sobre la pieza
- Parámetros programables del generador
- Control de profundidad
- Erosión orbital aplicaciones y características
- Líquidos dieléctricos
- Métodos de limpieza durante la mecanización
- Sistemas de fijación de piezas
- Dispositivos de las máquinas herramienta de:
UNIDAD DIDÁCTICA 3. PROCEDIMIENTOS PARA MECANIZADOS ESPECIALES
- Particularidades, aplicaciones y materiales mecanizables por:
UNIDAD DIDÁCTICA 4. ERRORES DE MEDICIÓN Y CONTROL DE VERIFICACIÓN
- Exactitud
- Precisión y apreciación
- Clasificación de los errores
- Relativo a los instrumentos de medición. Calibración, estado de conservación, uso inadecuado
- Debidos al verificador. Lectura falsa por error de paralelismo o presión de contacto incorrecta
- Como consecuencia de errores geométricos de la pieza
- Condiciones ambientales de temperatura, humedad,…
- Análisis de los errores y sus causas
- Periodicidad en la toma de medidas
UNIDAD DIDÁCTICA 5. CONTROL DE CALIDAD DEL PRODUCTO MECANIZADO
- Pautas de control
- Procesos estadísticos y generación de informes
- Conceptos básicos
- Representación gráfica
- Defectos típicos de calidad que presentan las piezas mecanizadas y las causas posibles de los mismos
UNIDAD DIDÁCTICA 6. MANTENIMIENTO DE MÁQUINAS (ENGRASE Y NIVELES)
- Objetivo de la lubricación
- Clasificación de los productos lubricantes
- Normas básicas para el engrase
- Sistemas de engrase
UNIDAD DIDÁCTICA 7. ACABADO EN LOS ÚTILES DE CONFORMADO
- Defectología y causas
- Limpieza de las piezas
- Ajuste de útiles
- Factores que afectan al desgaste de las herramientas
- Calidad en el corte
UNIDAD DIDÁCTICA 8. SISTEMAS DE AMARRE DE PIEZAS PARA EL MECANIZADO POR CORTE Y CONFORMADO
- Sujeción de las piezas según forma y dimensiones
- Obtención de formas por corte y conformado
- Amarre y centrado correcto
- Deformación plástica de los metales
UNIDAD DIDÁCTICA 9. PROCEDIMIENTOS DE VERIFICACIÓN Y MEDICIÓN EN EL MECANIZADO POR CORTE Y CONFORMADO
- Útiles de medición y verificación para control de piezas mecanizadas
- Instrumentos adecuados para verificación y medición
- Calibrados adecuados
- Dimensiones y estado superficial de la pieza
- Comparar resultados para verificación
UNIDAD DIDÁCTICA 10. REALIZACIÓN DEL PUNZONADO
- Definición y principios
- Etapas del punzonado: deformación, penetración y fractura
- Característica del borde cortado
- Máquinas herramientas para punzonado: prensas convencionales, prensas de CNC
- Fuerzas en el punzonado, resistencia de corte, fuerza de trabajo, compresión radial, fuerza de retroceso
- Factores que afectan al desgaste de la herramienta: material de trabajo, número de punzonadas, diámetro de punzón, juego de corte, lubricación
- Montaje de punzones y matrices
- Selección de la matriz en función del espesor de la chapa
UNIDAD DIDÁCTICA 11. REALIZACIÓN DEL PLEGADO
- Definición y principios
- Procesos de plegado: plegado al aire, fondo y acuñado
- Propiedades de las piezas plegadas
- Máquinas-herramientas en los procesos de plegado: plegadoras convencionales, plegadoras CNC
- Montaje, desmontaje y regulación de matrices y punzones
- Tabla de plegado
- Fuerza de plegado. Parámetros que la determina
UNIDAD DIDÁCTICA 12. ÚTILES DE CORTE Y CONFORMADO
- Modificaciones en matricería y moldes para corregir desviaciones en la calidad del producto obtenido
- Capacidades y limitaciones para la obtención de formas
- Otros procedimientos para la obtención de formas
- Riesgos en el manejo de equipos y máquinas
- Operaciones normales de acabado
- Procedimientos (limado, pulido, bruñido, lapeado…)
- Desgaste de la herramienta (material de trabajo, número de punzonadas, material de la herramienta, diámetro del punzón, juego de corte, lubricación)
UNIDAD DIDÁCTICA 13. PROCESOS DE CORTE DE CHAPA
- Definiciones de los siguientes procesos
UNIDAD DIDÁCTICA 14. TÉCNICAS DE OPERACIÓN DE CORTE POR PLASMA
- Tecnología del arco plasma
- Características del equipo y elementos auxiliares que componen la instalación de corte por arco plasma automática
- Gases plasmágenos: argón, hidrógeno, nitrógeno, aire
- Estado plasma de los gases: ionización
- Electrodos y portaelectrodos para el arco plasma: diámetros, longitudes, tipos
- Arco plasma: transferido y no transferido
- Temperaturas del arco plasma
- Variables fundamentales del proceso de corte por arco plasma: energía empleada, alta frecuencia
- Gases empleados
- Corte con plasma en mesa de agua
- Defectología del corte por arco plasma. Causas y correcciones
- Tiempos y calidad del corte con arco plasma
UNIDAD DIDÁCTICA 15. TÉCNICAS DE OPERACIÓN DE CORTE POR PLASMA
- Fundamentos del oxicorte. Principios de Lavoisier
- Tecnología del Oxicorte
- Características del equipo y elementos auxiliares que componen la instalación de oxicorte automático
- Gases empleados en oxicorte, características
- Retrocesos del oxicorte
- Válvulas de seguridad
- Presiones y consumos de los gases empleados
- Boquillas de caldeo y de corte
- Espesores a cortar
- Velocidad de corte
- Temperatura de la llama del soplete
- Empleo del propano en oxicorte para cortes de grandes espesores
- Defectos del oxicorte: causas y correcciones
- Tiempos y calidad del corte con oxicorte
UNIDAD DIDÁCTICA 16. OPERACIONES CON MÁQUINAS DE OXICORTE Y PLASMA AUTOMÁTICAS
- Máquinas de corte por lectura óptica
- Máquinas tipo pórtico automatizadas con CNC
- Elementos principales de una instalación automática
UNIDAD DIDÁCTICA 17. PREVENCIÓN ESPECÍFICA EN LOS PROCESOS DE MECANIZADO
- Riesgos de Manipulación y Almacenaje
- Identificar los riesgos en las instalaciones
- Elementos de Seguridad en las Máquinas
- Equipos de protección colectiva (las requeridas según el tratamiento superficial mecánico, químico o electroquímico)
- Equipos de protección individual (botas de seguridad, buzo de trabajo, guantes, gafas, casco, delantal)
Productos relacionados
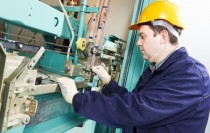
En el ámbito de la instalación y el mantenimiento, es necesario la instalación y mantenimiento de ascensores y otros equipos de elevación y transporte dentro del área profesional de maquinaria y...
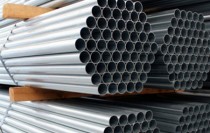
En el ámbito del mundo de la fabricación mecánica, es necesario conocer los diferentes campos sobre diseño de tubería industrial, dentro del área profesional de Construcciones mecánicas. Así, con...
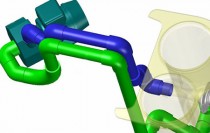
Hoy en día es importante saber desarrollar y conocer en profundidad aquella área en el que queremos trabajar o intervenir de un modo no solo profesional, sino también debido a intereses personales....
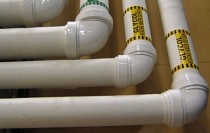
Hoy en día es importante saber desarrollar y conocer en profundidad aquella área en el que queremos trabajar o intervenir de un modo no solo profesional, sino también debido a intereses personales....
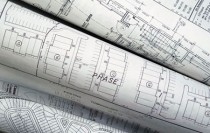
En el ámbito del mundo de la Fabricación Mecánica es necesario conocer los diferentes campos del Diseño de tuberías industrial, dentro del área profesional de Construcciones Mecánicas. Así, con el...
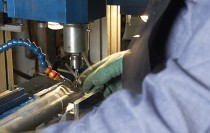
En el ámbito del mundo de la fabricación mecánica es necesario conocer los diferentes campos del mecanizado por arranque de viruta. Así, con el presente curso se pretende aportar los conocimientos...